Mixer le rigide et le souple pour des pièces bi-matières ou des surmoulages
Les géants de l’automobile BMW et Jaguar Land Rover – ainsi que de petits fournisseurs de pièces de rechange comme Minimizer – ont découvert depuis longtemps que l’impression 3D accélère à elle-seule la conception automobile et la fabrication. Cependant, les progrès significatifs des matériaux à disposition ont révolutionné les temps de développements.
Contexte
Les deux marques mondiales Jaguar et Land Rover sont désormais rassemblées sous l’aile britannique du groupe indien TATA. Jaguar Land Rover a installé une Objet Connex 500 il y a quelques années. Cette imprimante 3D a été choisie pour sa capacité multi-matériaux (rigide blanc opaque, transparent et souple).
À l’heure actuelle, huit lignes de véhicules sont produites par Jaguar Land Rover (JLR). Pour s’assurer que ces lignes maintiennent leur position privilégiée sur le marché, près de 20 % de la main-d’œuvre de Jaguar Land Rover est chargée du développement de produits, utilisant les techniques CAO les plus récentes, ainsi que le prototypage et l’outillage en interne pour réaliser les conceptions très rapidement.
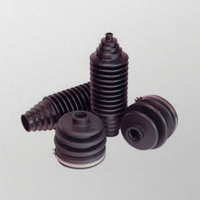
Jaguar Land Rover s’est doté de la Connex500 d’Objet pour étendre ses capacités de prototypage rapide à base de résine. La capacité de créer des modèles directement à partir de données CAO avec des matériaux élastomères et de type caoutchouteux, et de produire des mécanismes permet de réduire les cycles de développement. Pour prouver son efficacité, l’imprimante Connex d’Objet a d’abord été utilisée pour produire un assemblage complet de bouche de ventilation destiné à une Range Rover Sport. Cet assemblage a été modélisé à l’aide de matériaux rigides pour la cage et les valves de dérivation d’air, et de matériaux de type caoutchouteux pour les boutons de commande et l’étanchéité à l’air. Jaguar Land Rover a été en mesure d’imprimer la bouche ventilation intégrale, en tant que pièce de fonction, en une seule opération.
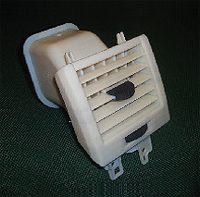
Jaguar Land Rover s’est doté de la Connex500 d’Objet pour étendre ses capacités de prototypage rapide à base de résine. La capacité de créer des modèles directement à partir de données CAO avec des matériaux élastomères et de type caoutchouteux, et de produire des mécanismes permet de réduire les cycles de développement. Pour prouver son efficacité, l’imprimante Connex d’Objet a d’abord été utilisée pour produire un assemblage complet de bouche de ventilation destiné à une Range Rover Sport. Cet assemblage a été modélisé à l’aide de matériaux rigides pour la cage et les valves de dérivation d’air, et de matériaux de type caoutchouteux pour les boutons de commande et l’étanchéité à l’air. Jaguar Land Rover a été en mesure d’imprimer la bouche ventilation intégrale, en tant que pièce de fonction, en une seule opération.
Après l’impression, le modèle a été testé immédiatement, démontrant que les charnières placées sur les valves étaient opérationnelles et que le bouton de commande présentait l’apparence et la sensation recherchées.
L’atout principal de la Connex est sa technologie de pulvérisation de résine 3D. En injectant jusqu’à 3 matériaux modèles distinctifs aux combinaisons présélectionnées au sein d’une structure de matrice, il est possible de créer plusieurs matériaux flexibles et rigides proposant diverses propriétés mécaniques et physiques, ainsi que plusieurs finitions.
En mode multi-matériaux, elle est utilisée pour une vaste gamme d’activité. Ces activités comprennent les concepts de style et de HMI (interfaces homme/machine), tels que les boutons, les interrupteurs, les porte-clés et toutes les pièces surmoulées.
Découvrez notre machine Objet Connex 3.